Digitalizing and automating a company's processes, or in other words, making a digital transformation, may sound like a grandiose project that turns the company's "normal" life completely upside down. Of course, the media often likes to highlight dizzying undertakings as examples, but in real life, the biggest triumphs often come from quite simple changes. One of these quick victories is the implementation of paperless work instructions or Standard Operating Procedures (SOPs), which, in turn, serve as a foundation for other automation steps.
SOPs are step-by-step written instructions for carrying out repetitive work tasks. In English, the process of setting up a procedure is vividly described by the "what, who, when, where, why" framework. Well-established SOPs reduce the possibility of human error in the production chain and ensure that employees perform their tasks efficiently, in the right order, on time, with high quality, safety, and in compliance with various regulations and standards.
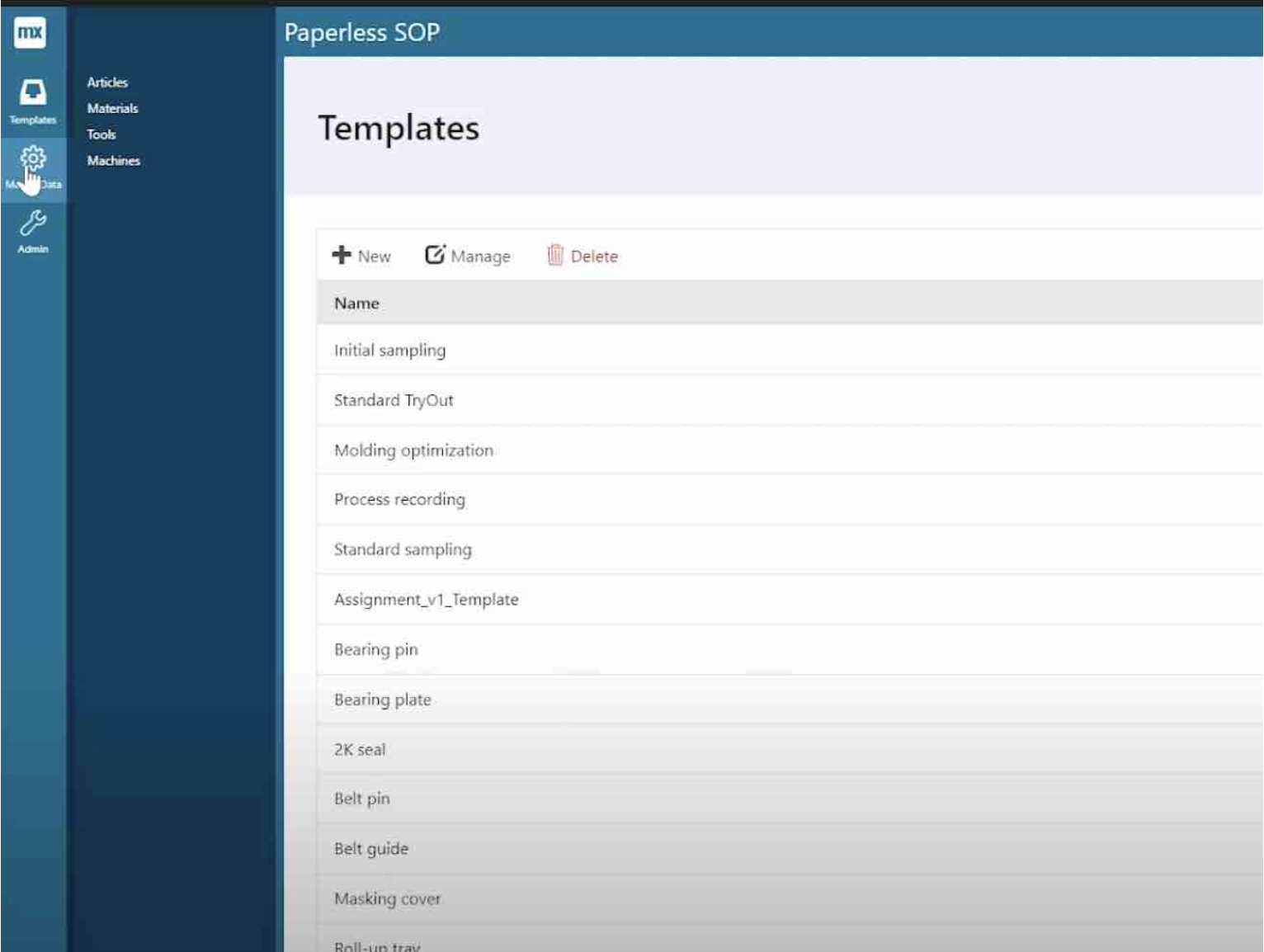
Precisely and timely documented work task instructions (SOPs) help to:
- work more efficiently and organizedly,
- improve and standardize the quality of products or services,
- cope with employee turnover more smoothly,
- teach new employees more effectively,
- increase confidence that the company's operations are carried out properly,
- and, of course, generate higher revenue thanks to all of the above.
Paperless SOPs are an opportunity for a leap in development
Paperless SOPs mean that work instructions are not located in a printed folder on the corner of a workbench, but are in digital format and usable in a digital system. However, paperless SOPs are not just a matter of format - they hide many opportunities for a significant development leap for the company.
- Compliance with paperless SOPs is more likely
SOPs are of no use if they are not used, fall behind, or disappear altogether. If compliance with work instructions depends on the employees' memory, people can become careless during busy times and following the instructions can easily be neglected. This can lead to (sometimes critical) errors, necessary steps being taken incorrectly, or even being forgotten altogether. Paperless SOPs are constantly available to employees and securely stored. Of course, the environment and technical possibilities for using SOPs must be considered to match the nature of the work, so that employees can actually use them during work (regardless of, for example, weather, dirt on hands, etc.).
In addition, paperless instructions can be associated with employee, device, or quality control activities so that the next work step cannot be started until certain actions are taken by the employee in the user interface (e.g. entering data, confirming an activity). Such linking of instructions to work steps further helps to ensure that the instructions are followed, which in turn ensures better quality of products and services.
- Paperless SOPs are easier to keep up-to-date
SOPs are recommended to be updated regularly at least every 6-12 months to reflect all changes made or that could be made to the instructions. Unlike paper pages, digital SOPs can be updated continuously and it can be ensured that the changes are reflected on all employees' desktops. Usually, there is also a record of changes made to paperless work instructions, so it is always possible to see when the instruction was changed and why, and to compare versions with each other.
- Paperless SOPs are the basis for streamlining and automating other processes
If SOPs are integrated with business process management software, it is easy to track production progress and see exactly which step is in progress and whether the work is following the plan or ahead or behind. It is also possible to track more accurately, for example, where bottlenecks occur and where or with whom errors tend to occur. Real-time comprehensive information is collected from all work steps, which can be used to analyze and optimize processes and can ultimately give the company a significant advantage.
Digitization of SOPs as a quick win for increasing competitiveness
In the digital transformation of a company, quick wins should not be underestimated - they may not necessarily be small victories. Relatively simple changes such as digitizing SOPs do not require a lot of resources, but the results are quickly visible and the investments quickly pay off. This is especially important for small and medium-sized enterprises, where every step must be precisely targeted to bring maximum possible benefit. In addition to the return on investment, quick wins are also good for maintaining motivation. Although digitization is more of a marathon than a sprint, successful pilot projects provide encouragement and input for taking on larger challenges.
Digitalizing SOPs with Mendix software quickly and effortlessly
Mendix is Siemens' low-code platform that allows for the quick creation of structured SOPs that can be used immediately as work instructions. Mendix platform supports an iterative approach, which is commonly used in software development. The central principle of the iterative approach is to create the simplest solution possible, which is then gradually improved through continuous feedback cycles. The advantage of this method is that the solution is developed in small steps, stakeholders can constantly provide feedback, and changes can be made while they are still easy to implement.
With Mendix, you can:
- Map and capture work instructions as a template,
- Test the initial template in production and quickly gather feedback,
- Supplement the work instructions if needed and use the final work instructions as an SOP,
- Use SOPs for production planning and issuing work orders,
- Continuously improve SOPs based on feedback or changing needs or regulations.
The key to Mendix's approach is effective communication. With paper-based work instructions, communication tends to be one-way, and problems, malfunctions, or proposals from production may not reach the management level. If a step does not produce the desired outcome or an employee sees other areas for improvement, perhaps some steps could be skipped altogether or tasks performed in a different order? If providing feedback is difficult, such suggestions are likely to go unreported, or the employee may simply not follow the instructions.
How paperless SOP creation looks like in Mendix
- The administrator creates a template for the standard operating procedure (SOP) that includes a set of predetermined tasks to be completed in a specific order. Each task consists of a name and a simple description, but may also include supporting instructions, diagrams, and parameters.
- The project manager sends the SOP template for production testing.
- The system guides the operator step by step through the task completion process. If the operator encounters any issues or errors, they can inform the project manager. The operator enters all necessary values and other relevant information, confirms the task, and submits it for review.
- The project manager checks the task performance and can update the instructions or confirm it as an SOP.
- Based on the SOP, production tasks can be created automatically and sent to the operator's workspace. The SOP fields are pre-filled with the values entered during testing, but it is also possible to inform the project manager of any issues or suggestions for changes.
The benefits of Mendix's paperless SOPs in addition to continuous communication and operational feedback are:
- Clarity - all SOPs have a clear lifecycle: "draft," "active," and "archived." At any given stage of the process, there can only be one active template. To make changes to an SOP, a new draft can be created based on the active template, where steps can be modified, deleted, or added. When the administrator is ready to make the changes, they can publish the template, which turns the draft into an active template and archives the previous active template.
- Multilingual support - when creating templates, parameters and instructions can be translated into multiple languages in parallel, so users can choose their preferred language. This means that all company templates are centrally created, saved, and coordinated, and production managers can be sure that all employees with different languages or in different production locations around the world use the same templates.
- Support for different screens - Mendix's desktop can be used on various mobile devices, so all employees can use it during their work.
- Overview of the workflow - both the project manager and the operator can see a complete overview of their past, current, and completed tasks, and the production manager can keep track of the workflow.
The result is higher quality and more consistent results, more efficient production, and better management decisions.
How long does it take to implement paperless SOPs?
Of course, this depends on the complexity of the production processes. The project duration could range from 1 to 3 months, with most of the time spent on change management and learning new practices.
Processa Technologies is Siemens Mendix's partner in the Baltics. Mendix is a low-code platform that allows for 7-10 times faster process automation through software and is ideal for digitizing production processes and creating integrations.